Understanding Injection Molded Prototypes: An In-Depth Guide
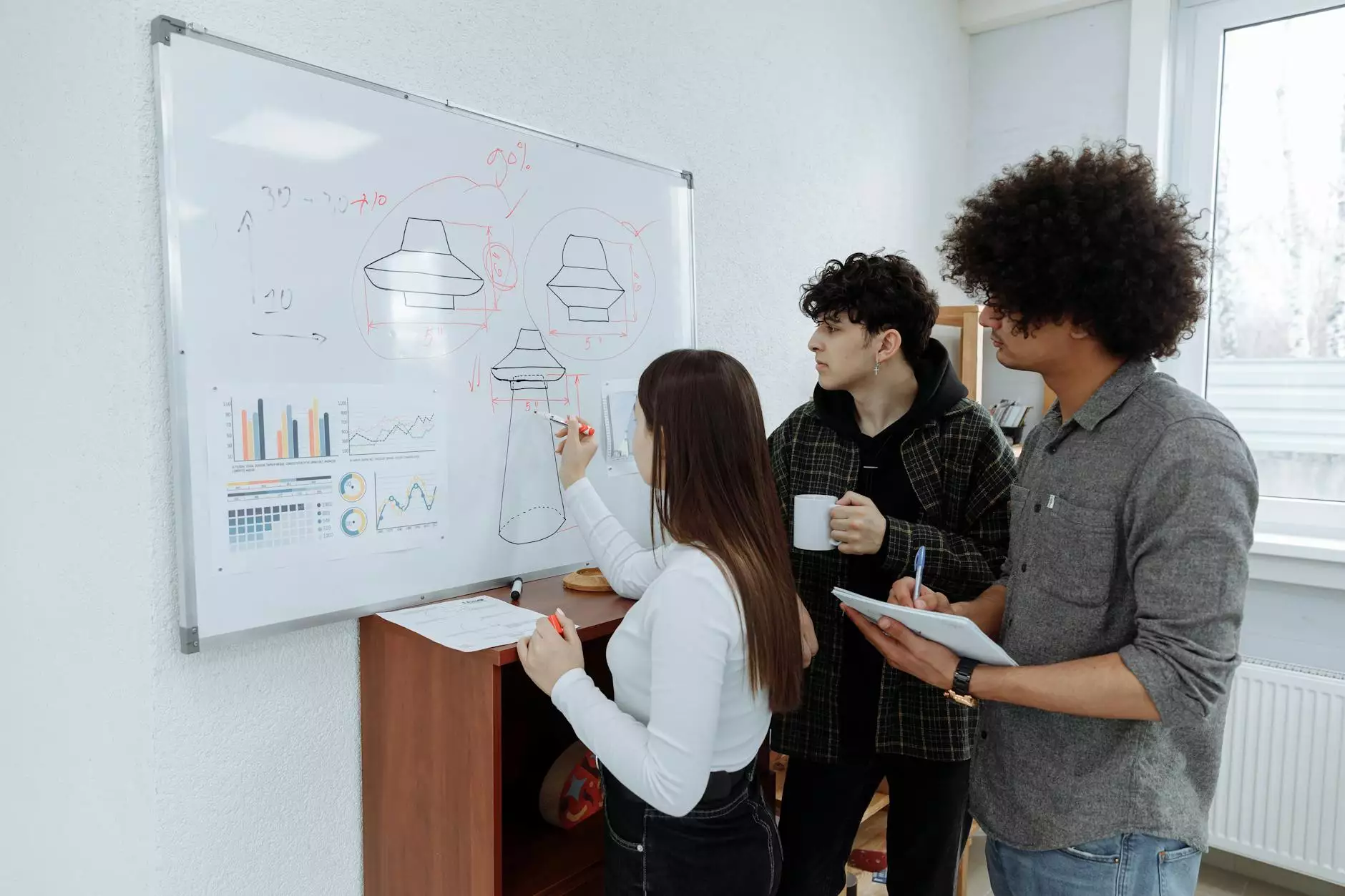
In today's fast-paced market, the demand for innovative products and rapid prototyping is at an all-time high. One of the most efficient ways to bridge the gap between conception and production is through Injection Molded Prototypes. This article dives deep into the intricacies, advantages, and applications of injection molded prototypes, especially in the realm of metal fabrication.
What Are Injection Molded Prototypes?
Injection Molded Prototypes are preliminary versions of products created through the injection molding process, which involves injecting molten material into a mold to create a specific shape. These prototypes allow designers and engineers to test and evaluate their products before moving into mass production. By utilizing this technique, businesses can save time, reduce costs, and enhance the efficiency of their production processes.
The Importance of Prototyping in Product Development
Prototyping serves as an essential step in product development. Here are several reasons why:
- Visual Representation: Prototypes provide a tangible representation of a product, making it easier to visualize the end result.
- Functionality Testing: They allow engineers to test the functionality of a design, identifying flaws before mass production.
- Material Analysis: Prototyping helps in evaluating the performance of materials, ensuring the right choice for the final product.
- Cost Reduction: Early identification of design issues can lead to significant cost savings.
- Market Feedback: Physical prototypes enable businesses to gather valuable feedback from stakeholders and potential customers.
The Process of Creating Injection Molded Prototypes
The process of creating Injection Molded Prototypes is meticulously designed to ensure precision and quality. Here's a step-by-step breakdown:
1. Design and CAD Modeling
The first step involves creating a detailed design of the product using CAD (Computer-Aided Design) software. This digital representation allows designers to tweak and modify the design before it enters the prototyping phase.
2. Mold Fabrication
Once the design is finalized, a mold is fabricated, usually from steel or aluminum. This mold is essential as it dictates the shape and quality of the final product. High-quality molds are crucial for producing high-fidelity prototypes.
3. Injection Molding Process
In this stage, the molten material is injected into the mold under high pressure. After the material cools and solidifies, the mold is opened to reveal the finished prototype. This process can be repeated as many times as necessary to create multiple prototypes.
4. Finishing Touches
After the molding process, prototypes may require additional finishing steps such as sanding, painting, or texturing, depending on the specifications of the prototype.
Advantages of Injection Molded Prototypes
Utilizing Injection Molded Prototypes offers several compelling advantages:
- Rapid Production: The speed of creation allows companies to move swiftly from design to evaluation.
- Cost-Effectiveness: By reducing the need for extensive tooling and labor, businesses can cut down on initial costs.
- Scalability: Once a prototype is validated, scaling up to mass production is seamless and efficient.
- High Precision: The injection molding process delivers prototypes with tight tolerances and intricate details, mirroring the final product closely.
- Diverse Material Options: Various materials can be used for prototyping, including thermoplastics and metals, catering to a wide range of applications.
Applications of Injection Molded Prototypes in Various Industries
Injection Molded Prototypes are relevant across multiple sectors, including:
1. Automotive Industry
In the automotive sector, prototypes are crucial for testing parts such as dashboards, panels, and structural components. Manufacturers use these prototypes to ensure that components fit correctly and perform as intended.
2. Consumer Electronics
For companies creating electronic devices, rapid prototyping helps in assessing the ergonomics and functionality of the product. Injection molded prototypes allow for real-world testing and user feedback collection.
3. Medical Devices
In the healthcare sector, the integrity of medical devices is paramount. Prototypes are used extensively to ensure that devices are safe and functional for users before entering production.
4. Industrial Equipment
Industrial equipment manufacturers rely on prototypes to test the durability and reliability of their products under various conditions. This ensures quality assurance prior to widespread distribution.
5. Consumer Products
Many consumer products, including household items and toys, undergo prototyping to facilitate market testing and ensure alignment with consumer expectations.
Considerations When Using Injection Molded Prototypes
While Injection Molded Prototypes present numerous benefits, there are also key considerations:
- Initial Setup Costs: The costs of creating molds can be significant, but these costs often pay off with efficient mass production.
- Time for Mold Creation: Creating a mold can take time, especially for complex designs, which could delay prototypes.
- Limited Material Properties: Some prototype materials do not perfectly replicate the final production material, which can impact testing.
Choosing the Right Partner for Your Prototyping Needs
Partnering with a reputable and experienced manufacturing firm is vital for optimal outcomes. Here are some factors to consider when selecting a partner:
1. Industry Experience
Look for partners with a proven track record in your specific industry. They will be better equipped to understand your needs and provide tailored solutions.
2. Technological Capabilities
A partner with advanced machinery and technology can ensure high-quality prototypes produced efficiently.
3. Material Options
Inquire about the range of materials they offer for injection molding. A diverse selection allows you to test various prototype characteristics.
4. Customer Support
Effective communication and support throughout the prototyping process can make a substantial difference in outcome. Opt for partners who prioritize customer satisfaction.
Conclusion: Embracing Innovation with Injection Molded Prototypes
In conclusion, Injection Molded Prototypes are indispensable tools in modern product development and manufacturing. By enabling rapid prototyping, testing, and validation, businesses are better positioned to meet market demands while minimizing risks and costs. As industries continue to evolve, leveraging the advantages of injection molded prototypes will undoubtedly play a pivotal role in the success of future innovations. Embrace this technology and watch your ideas transform into reality with unmatched speed and efficiency.