Precision Injection Molding: Revolutionizing Metal Fabrication
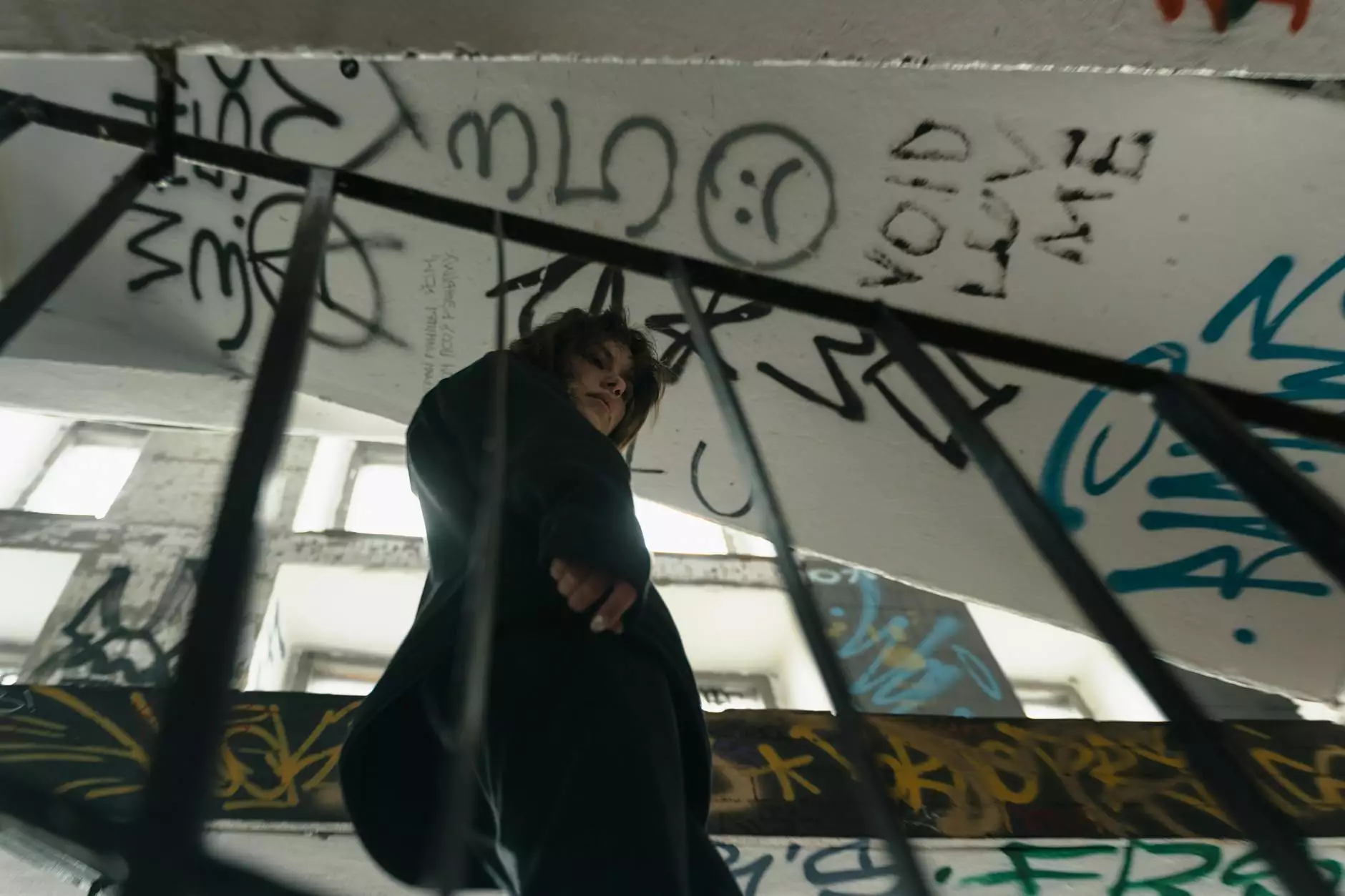
Precision injection molding has emerged as a game-changer in the world of manufacturing, especially within metal fabrication. This advanced technique allows for the creation of complex shapes and components with high dimensional accuracy, paving the way for innovations across various industries. In this comprehensive article, we will delve into the intricacies of precision injection molding, exploring its applications, benefits, and the future it holds for businesses like DeepMould.net.
The Basics of Precision Injection Molding
At its core, precision injection molding involves injecting molten material into a precision-engineered mold. This process is primarily used for producing intricate components and is widely favored for its ability to produce parts with remarkably low tolerances. The following steps outline the injection molding process:
- Material Selection: The first step is choosing the right material for the specific application. Options include metals, plastics, and composites.
- Molding Design: Engineers create precise molds that conform to the desired specifications of the end product.
- Injection Process: Molten material is injected into the mold under high pressure.
- Cooling: The material is allowed to cool and solidify, taking the shape of the mold.
- Demolding: The molded part is removed from the mold, completing the process.
Why Precision Injection Molding Matters
The importance of precision injection molding cannot be overstated, especially when it comes to industries that demand high-quality products. Here are several reasons why this technology has become fundamental in metal fabrication:
- High Precision and Accuracy: The manufacturing process achieves tolerances as fine as ±0.001 inches, making it ideal for applications requiring exact fits and finishes.
- Cost Efficiency: Once the initial set-up costs are covered, the mass production of parts becomes significantly more cost-effective compared to traditional manufacturing methods.
- Complex Geometries: Molding can produce parts with intricate designs that would be difficult, if not impossible, to create using other techniques.
- Material Versatility: The process is compatible with a variety of materials, including high-strength metals, engineering plastics, and more.
- Sustainability: Modern techniques have led to reduced waste during manufacturing, contributing to greener production practices.
Applications of Precision Injection Molding
The applications of precision injection molding are vast and span multiple industries. Here are some notable examples:
Aerospace Industry
In the aerospace sector, where weight and precision are critical, precision injection molding is used to create components such as brackets, housings, and panels with minimal weight yet robust strength.
Automotive Industry
The automotive world utilizes the technology to produce lightweight yet durable components that contribute to overall vehicle efficiency and performance. Parts like casings, clips, and fuel system components benefit from injection molding.
Consumer Electronics
High-tech gadgets require the precision production of small, intricate parts, making them prime candidates for injection molding. Connectors, casings, and buttons are often manufactured this way.
Medical Devices
The medical industry demands the utmost precision for devices like surgical instruments and housings for diagnostic equipment. Injection molding meets these stringent requirements with ease.
Defense Sector
Similarly, defense applications require parts that can withstand rigorous environments. Precision injection molding provides the reliability needed for components in various military equipment.
Benefits for Businesses at DeepMould.net
For businesses like DeepMould.net, specializing in precision injection molding and metal fabrication, the advantages of this technique are undeniable. Here’s how embracing this technology can enhance operations:
Enhanced Product Quality
Utilizing precision injection molding results in higher-quality products. The ability to produce consistent parts with minimal defects leads to improved end-user satisfaction.
Faster Production Times
Speed is a significant factor in manufacturing. Injection molding allows for rapid production cycles, enabling businesses to meet market demands promptly.
Lower Production Costs
By reducing scrap rates and maximizing material usage, precision injection molding can lead to considerable cost savings for manufacturers.
Innovation Opportunities
Engineers and designers can leverage this technology to create innovative products, pushing the boundaries of what is possible with traditional methods.
The Future of Precision Injection Molding
As technology continues to advance, the future of precision injection molding looks promising. Here are some trends and forecasts:
Integration with Additive Manufacturing
The fusion of traditional injection molding with 3D printing techniques offers new possibilities for creating molds, particularly for rapid prototyping and limited runs.
Increased Automation
The shift towards automation in manufacturing will lead to higher efficiency rates. Smart systems can monitor the injection process in real time, making adjustments as necessary.
Sustainable Practices
As sustainability becomes a focal point for businesses across all sectors, the push for eco-friendly materials and processes will shape the future of injection molding. This includes using recycled materials and adopting energy-efficient practices.
Conclusion
In summary, precision injection molding stands as a cornerstone of modern manufacturing, particularly in the realm of metal fabrication. With its myriad applications, benefits, and the promise of continued innovation, it is clear why companies such as DeepMould.net are investing in this technology. By harnessing the power of injection molding, businesses are not only enhancing their production capabilities but also ensuring a competitive edge in an ever-evolving market. As we look to the future, it is evident that precision injection molding will continue to play a vital role in shaping the manufacturing landscape.