The Power of Rapid Prototype Mold in Modern Manufacturing
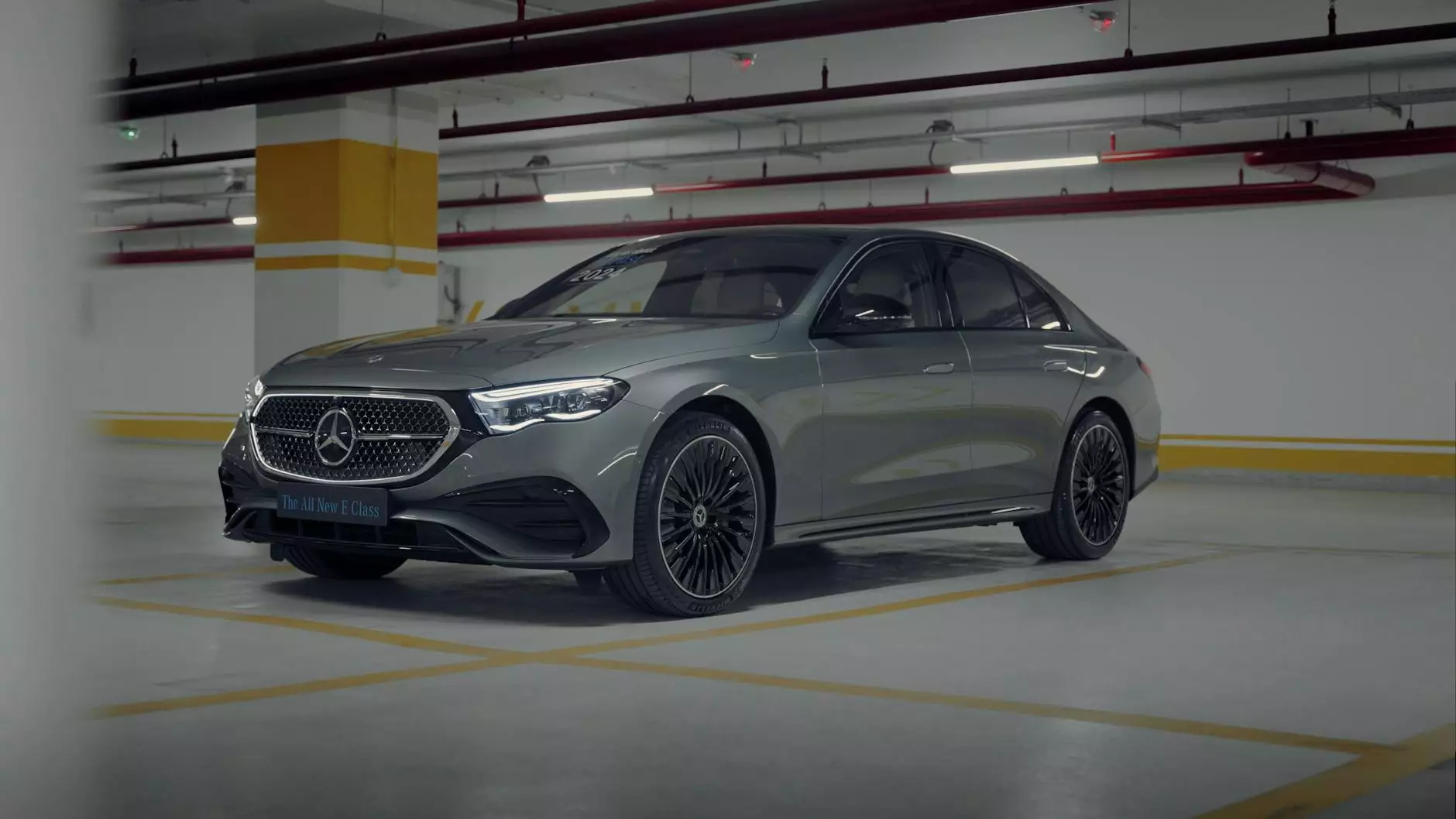
In today's fast-paced industrial environment, the demand for effective and efficient manufacturing processes has never been greater. One of the most revolutionary innovations that has emerged to meet these demands is rapid prototype mold technology. This transformative approach not only speeds up the production process but also significantly lowers costs, improving overall product quality. In this article, we will explore the various aspects of rapid prototype mold, its advantages, applications, and how businesses like DeepMould are leveraging this technology to stay ahead in the competitive landscape.
Understanding Rapid Prototype Mold
Rapid prototype mold refers to a process that enables manufacturers to quickly create molds for prototypes that can be tested and evaluated before mass production. This process predominantly involves advanced manufacturing technologies such as 3D printing, CNC machining, and injection molding, which allow for the rapid development of prototypes without the need for extensive lead times typically associated with traditional manufacturing methods.
The essence of rapid prototyping lies in its ability to streamline the design process. Designers and engineers can quickly iterate on their designs, receiving feedback and making adjustments in real-time, leading to a more refined final product before entering full-scale production.
Advantages of Rapid Prototype Mold
The benefits of utilizing rapid prototype mold technology are profound, directly influencing both efficiency and cost-effectiveness in manufacturing. Here are some of the key advantages:
- Speed: One of the most significant advantages is the drastic reduction in manufacturing time. Prototypes that once took weeks to produce can now be created in a matter of days.
- Cost Efficiency: By reducing the time and materials required for creating prototypes, companies save significantly on production costs.
- Design Flexibility: Rapid prototyping allows for easy modifications and iterations, enabling teams to pivot quickly based on feedback and testing.
- Risk Mitigation: Testing prototypes before full-scale production minimizes the risk of costly mistakes, ensuring that the final product meets market demands.
- Enhanced Collaboration: Designers, engineers, and other stakeholders can collaborate more effectively with tangible prototypes, fostering innovation.
Applications of Rapid Prototype Mold in Various Industries
Across various sectors, the impact of rapid prototype mold technology is being felt, leading to significant advancements in product development and manufacturing. Here’s a look at some of the industries harnessing this technology:
1. Automotive Industry
In the automotive sector, rapid prototyping plays a crucial role in developing new vehicle models. Manufacturers can quickly prototype components, testing them for fit and function before going into mass production. This leads to more innovative designs and enhanced safety features, while reducing time-to-market for new vehicles.
2. Aerospace Sector
The aerospace industry is another field where precision and reliability are paramount. Rapid prototype mold allows engineers to produce parts that meet stringent safety and performance standards. Early prototypes can be tested extensively, ensuring that the final components perform reliably in demanding conditions.
3. Consumer Goods
For companies producing consumer goods, rapid prototyping enables faster product launches and the adaptation of designs based on market trends. Manufacturers can create multiple versions of products quickly, effectively tailoring their offerings to consumer preferences.
4. Medical Devices
In the medical field, rapid prototype molds are vital for developing and testing medical devices. Prototyping allows for a better understanding of how devices will behave in real-world scenarios, ultimately leading to safer and more effective healthcare solutions.
Choosing the Right Materials for Rapid Prototype Mold
The selection of appropriate materials is critical in the rapid prototype mold process. The right material not only affects the quality of the prototype but also its performance during testing. Here are some common materials used in rapid prototyping:
- Thermoplastics: These materials are widely used due to their versatility and ease of molding. They offer high impact resistance and can be recycled.
- Resins: Suitable for 3D printing, resins can produce incredibly detailed prototypes and are often used in industries that require precise models.
- Metals: For metal prototyping, materials like aluminum and stainless steel are commonly used, offering strength and durability for functional testing.
- Composite Materials: These materials are becoming increasingly popular due to their strength-to-weight ratio, making them ideal for industries such as aerospace and automotive.
The Future of Rapid Prototype Mold
The future of rapid prototype mold is incredibly promising. As technology continues to advance, we can expect several transformative trends:
- Increased Automation: The rise of automated systems will streamline the rapid prototyping process further, reducing errors and enhancing speed.
- Integration with AI: Artificial intelligence can assist in optimizing designs and predicting potential failures in prototypes, leading to smarter manufacturing practices.
- Sustainability Focus: As environmental concerns grow, more businesses are looking for sustainable materials and processes, leading to innovations in eco-friendly rapid prototyping.
Conclusion: Embracing Rapid Prototype Mold for Competitive Advantage
In conclusion, the utilization of rapid prototype mold technology is not just a passing trend; it is rapidly becoming a fundamental component of modern manufacturing strategies. Companies today, especially in competitive industries such as automotive, aerospace, consumer goods, and medical devices, must embrace this technology to innovate and streamline their processes. With enhanced speed, reduced costs, and improved product quality, organizations like DeepMould are setting a precedent for what is possible when leveraging advanced prototyping techniques. The future is bright for those who adopt rapid prototype mold as a key element in their business strategy, ensuring they remain at the forefront of their industries.