Components of Injection Moulding Machine
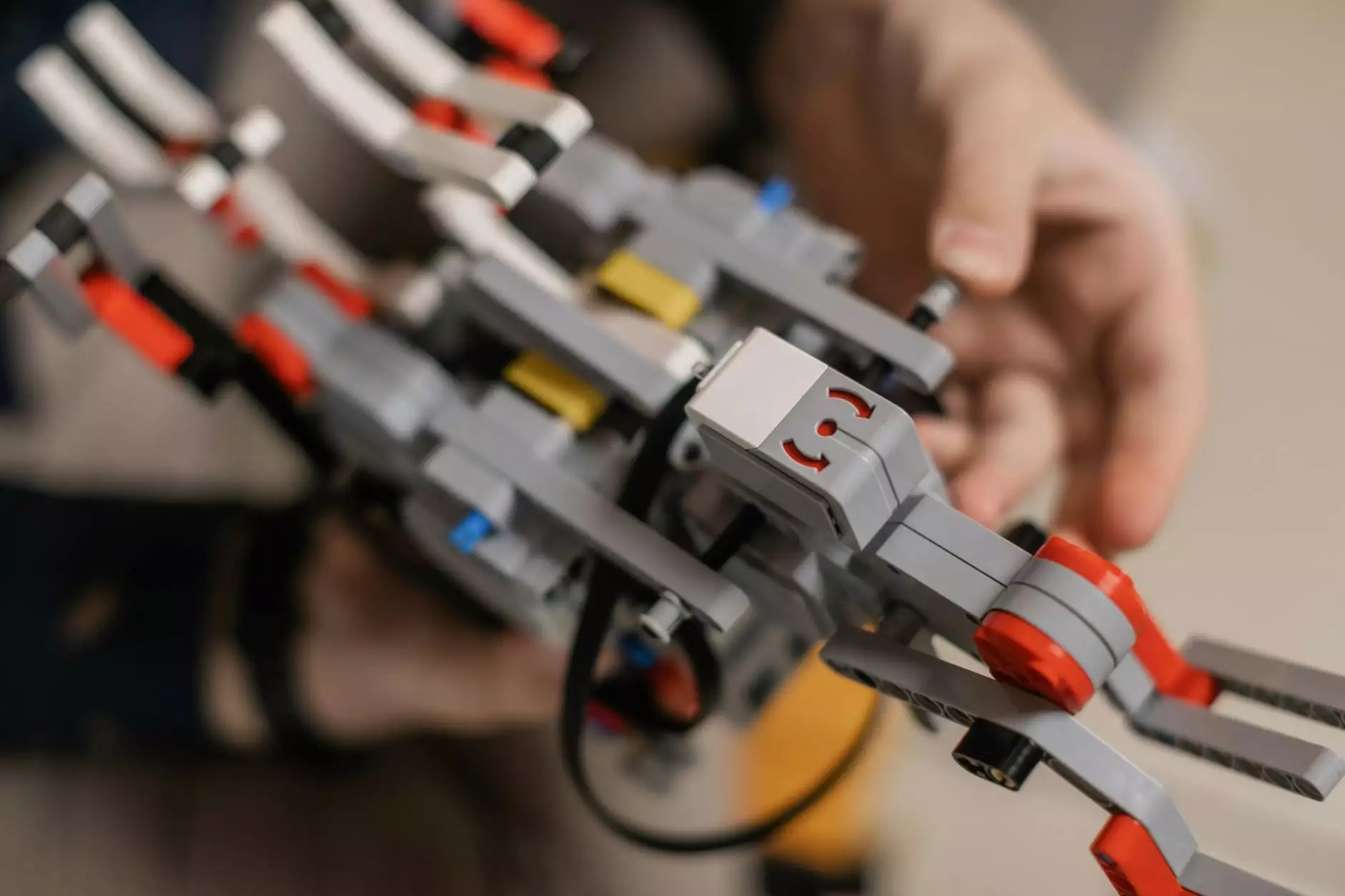
Injection moulding machines play a crucial role in the manufacturing industry, allowing businesses to produce various products efficiently and with precision. Understanding the different components of an injection moulding machine is essential for optimizing its performance and ensuring high-quality output.
1. Injection Unit
The injection unit is responsible for melting and injecting the raw material into the mould cavity. It consists of the screw, barrel, and nozzle. The screw rotates within the heated barrel, melting the material as it moves forward. The nozzle controls the flow and direction of the molten material into the mould.
2. Clamping Unit
The clamping unit holds the mould in place during the injection process. It provides the necessary force to keep the mould closed and ensures accurate and consistent product dimensions. The clamping unit consists of the clamping mechanism, mould opening and closing system, and hydraulic or mechanical drive system.
3. Mould or Die
The mould, also known as the die, shapes the molten material into the desired product form. It is made from durable materials such as steel and contains two halves, the core, and cavity. The core creates internal features, while the cavity defines the product's outer shape.
4. Heating and Cooling System
The heating and cooling system ensures precise temperature control throughout the injection moulding process. It consists of heaters that melt the raw material and cooling channels that solidify the material quickly after injection. Maintaining optimal temperature control helps prevent defects and ensures consistent part quality.
5. Control System
The control system monitors and controls the entire injection moulding process, including temperature, pressure, speed, and timing. It allows operators to adjust parameters to achieve the desired product properties and minimize production errors. Modern machines often feature advanced computerized control systems for enhanced accuracy and efficiency.
6. Ejection System
The ejection system removes the final product from the mould once it has solidified. It typically includes ejector pins, sleeves, and plates that apply force to push the product out of the mould. Proper ejection system design is vital to avoid damage to the product and maintain production efficiency.
7. Hydraulic System
The hydraulic system powers the movement of various machine components, such as the clamping unit and injection unit. It uses hydraulic pumps, motors, and valves to generate and control hydraulic pressure. The hydraulic fluid is responsible for transmitting power and lubricating moving parts.
8. Auxiliary Equipment
Injection moulding machines may also require additional auxiliary equipment to support the manufacturing process. This can include material dryers, hopper loaders, temperature controllers, and robots for automation. These auxiliary systems improve efficiency, reduce downtime, and enhance overall productivity.
Conclusion
The components of an injection moulding machine work together seamlessly to produce high-quality products quickly and efficiently. Understanding how each component functions and their importance in the manufacturing process enables businesses to optimize their operations and deliver exceptional results.
At QuickParts.com, we specialize in providing top-notch metal fabrication services and cutting-edge 3D printing solutions to meet your business's unique needs. Our team of experts is dedicated to delivering high-quality results, utilizing the latest technologies and ensuring customer satisfaction. Contact us today to learn more about our services and how we can support your business.
components of injection moulding machine